The Bottom Line:
- Labor shortages create obstaclesy
- Technology overcomes pandemic challenges
- Virtual reality and augmented reality use increasing
Automation can transform a bakery production environment—improving speed and efficiency, reducing labor costs, and decreasing safety risks to staff. Despite the advancements in technology, human intervention often is required—to check on processes, fix glitches, and more. However, the human required to save the day can’t always be physically present to watch and intervene.
Remote monitoring technology can help bridge the distance between person and process, putting the right solution within reach, even when expert help is miles away.
Remote support
While remote monitoring and control technology has advanced in recent years, the technology itself is not new.
“Since most of our systems incorporate an integrated control system this has enabled us to provide remote monitoring and troubleshooting of systems for over 20 years; this can be accomplished through VPN access or in cases where this isn’t available or desired through cellar communications,” says Scott Houtz, president, Air Management Technologies, Lewisburg, PA. “In the case of alarming and critical information sharing, push notifications via email and cell phones can be provided to eliminate the need for extensive monitoring.”

Angela McDaniel, marketing coordinator with Formost Fuji, Woodinville, WA, says the company’s horizontal flow wrappers, horizontal bagging machines, and other automated packaging equipment comes with human-machine interfaces (HMIs) designed to help operators get up to speed quickly. They also use augmented reality (AR), virtual reality (VR), and similar tools to help operators as needed.
“This technology is also now commonly being used for factory acceptance tests (FATs),” she says. “We’ve done the full gamut from putting a tablet up and using FaceTime to HoloLens glasses. We have also had customers send out their custom system that had a camera, headphones, and all equipment necessary for virtual communication.”
McDaniel adds that while in-person FATs still seem to be the norm, “handling them digitally means that more people can be involved and now that companies are more comfortable with AR/VR, it has become a dependable option if travel is an issue.”
Technology in action
Like Formost Fuji, other companies are finding AR, VR, and other emerging interactive technology useful in remote applications.
“At tna, we’re always looking for ways to harness the latest developments in digital technology to improve efficiencies in food production and processing,” says Juan Del Real, aftermarket sales manager at tna solutions North America, Coppell, TX.
One of the most recent remote technology offerings from tna is its Remote Assist Service. “Powered by the Microsoft HoloLens 2 headset, it leverages AR technology to allow tna engineers to connect and collaborate with customers virtually in real-time and remotely guide machine maintenance, installation, training, and servicing. This allows for an entirely digitally enhanced customer service experience, giving food manufacturers the tailored support they need to keep lines operating smoothly—wherever they are in the world.”

Bühler Group (Uzwill, Switzerland) offers remote support via a combination of “smart” glasses and AR software, enabling customers to troubleshoot mechanical challenges with help from a distance.
“The customer can wear voice-control smart glasses while having the call with Bühler’s expert; through the glasses, we can see what is happening on-site and give customers guidance via voice or by showing the drawings or marks on video stream,” says Sue Xuechun Yang, business development manager, customer service for consumer foods, Bühler Group. The customer can interact with the support expert—listen to their voice, see their guidance through the glasses, and follow their guidance to adjust the equipment as necessary.
“With that kind of solution, there is no need to travel to customer sites and still support the customer on many mechanical or operational issues,” Yang advises.
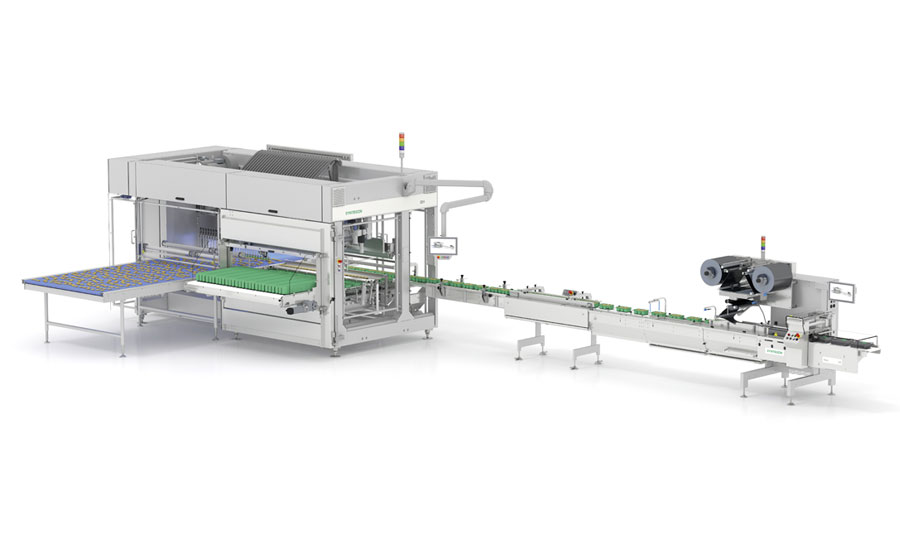
Earlier this year, Syntegon Packaging Technology (New Richmond, WI) launched Synexio, a service that enables the company to remotely monitor the status and performance of equipment, sharing a visual representation to customers via a dashboard.
“By using different communication channels and tools, we can, for instance, connect to and troubleshoot customer`s machines remotely, given they are connected to the service,” explains Christian Munzinger, product management customer service, Syntegon.
Additionally, Munzinger says, the company is working on a standardized Visual Assistance solution for remote support; powered by Microsoft Hololens technology, the solution will empower remote support interaction with customers in the event of mechanical equipment issues.
Many equipment companies offer remote solutions integrated into their equipment. For example, tna recently launched its robag 3e vertical form, fill, and seal packaging system (geared toward bakery and snacks operations) with features like standard EtherCAT real-time protocol, smart diagnostics, and remote connectivity capabilities.
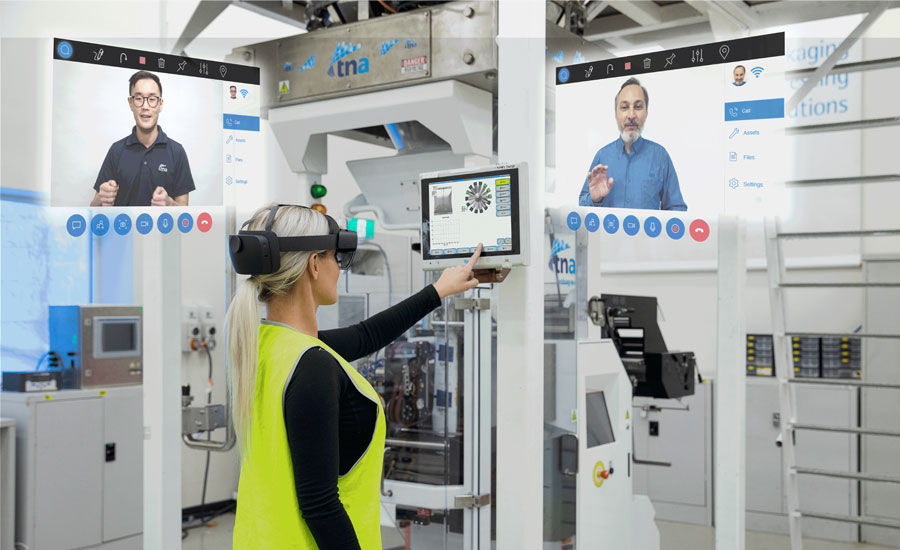
“By offering these features, we give manufacturers the opportunity to optimize their lines in real-time with detailed packaging performance reports,” says Del Real. “When challenges do arise the system’s smart operating system and remote communication features give operators access to targeted global servicing support to get production back up and running quickly and easily.”
Pandemic impact
The global pandemic had a tremendous impact on the bakery industry, making remote equipment monitoring and technical support more appealing. However, companies that had such solutions in place and in action prior to the arrival of the virus often found the shift was less dramatic than those who had not implemented such solutions beforehand.
Rick Gessler, vice president of engineering, Delkor Systems, Minneapolis, MN, says the company has offered solutions for remote support tailored to a specific customer’s needs, ranging from basic phone-based support desk to “dial-in” VPN remote service agreements with remote troubleshooting capabilities. “The pandemic had minimal impact to our support structure other than more in-depth phone discussions prior to dispatching service,” he says. “Most service/equipment issues on modern robotic packaging lines can be resolved with phone support and/or a VPN connection to the machine.”
Yang says Bühler had been emphasizing remote automation support prior to the pandemic. After the arrival of COVID-19, though, Bühler, like its clients, had to adapt.
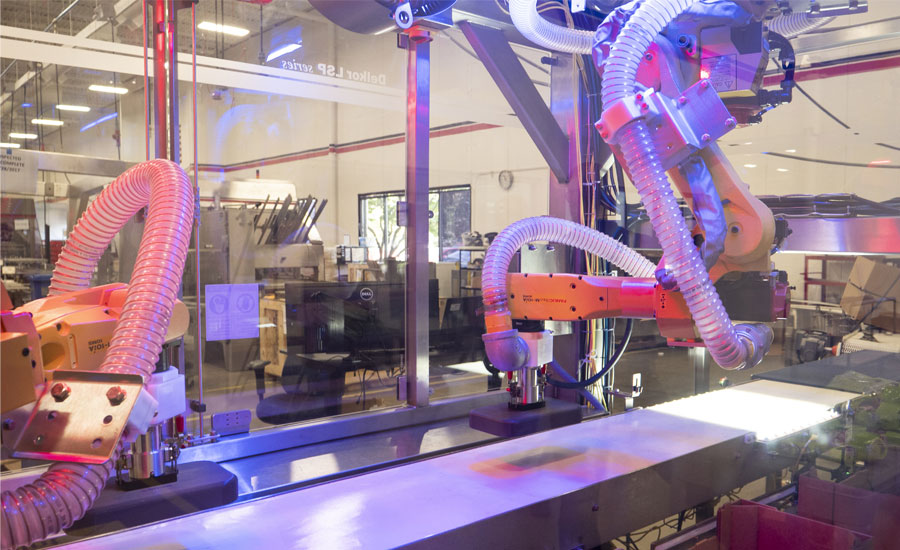
“On the one hand, it was not that easy to travel on-site anymore, therefore, the teams had to find alternative solutions to support customers worldwide. On the other hand, customers had to adapt to the new situation and became more open to use digital technology, like smart glasses, and got more used to meeting remotely,” she says. “All these remote communication tools have also improved significantly.”
Yang adds that since the company has expanded its remote business support in to mechanical areas, using tools like smart glasses and interactive communication software, Bühler teams are able to guide customers remotely by voice, drawings, step by step, to solve their mechanical issues.
Moving forward
The effectiveness of remote solutions, Gessler advises, is greatly helped by the people facilitating.
“Delkor has a large reserve of highly skilled technicians that staff our help desk and that are available to assist our customers through any issues they may experience,” he remarks. “The most important part of any type of remote support is having a knowledgeable resource on the other end of the line.”
And while the people help the remote technology, Gessler adds, the technology also can help the people.
“We are continuing to look for solutions to decrease travel requirements and increase the value to our clients,” says Houtz. “It’s a win-win situation when you can provide hands-on local support at a reduced cost with remote oversight to assure that systems are delivering expected performance.”
Del Real predicts that while remote technologies have made great strides, their full potential in serving the bakery and snacks industry is yet to be realized.
“Our current focus is on harnessing them to support day-to-day plant operations, providing preventive solutions and training, but the possibilities are far-reaching,” he says. “Aside from improving production efficiency, product quality and consistency, remote support solutions have the potential to connect brands to consumers and provide information on the ingredient sourcing and manufacturing process, improving consumer trust and loyalty.”
McDaniels predicts that, “As virtual technology becomes mainstream and the costs for the equipment becomes more affordable, many companies will find more ways to use AR/VR to interact with customers, whether it be for sales or service support.”